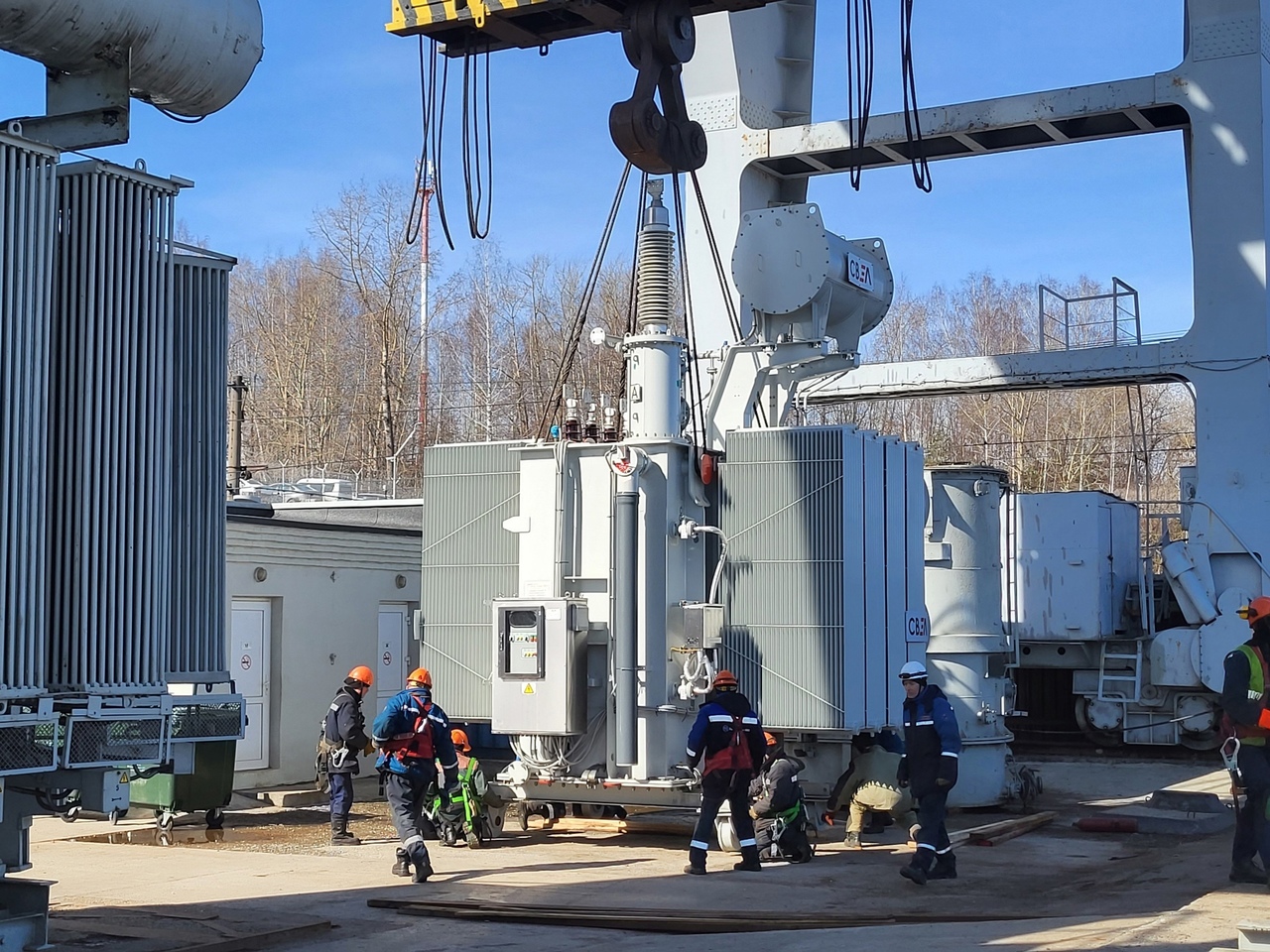
Special Transformer Replacement with NERM Panel, ZORC, and ADIT System
Challenge:
The client’s 1000kW dry-type transformer, which featured an outdated NERM panel from an obsolete OEM, was facing significant reliability and efficiency issues. The transformer was situated in a constrained footprint, complicating the replacement process. The key challenges were to identify a modern replacement that fit within the existing physical constraints and offered enhanced functionality and durability. The obsolete system lacked contemporary diagnostic capabilities and protective measures, leading to increased risk of system failure and frequent maintenance issues.
Solution:
To address these challenges, we partnered with a power systems integrator with expertise in transformer design. Our solution involved sourcing a new transformer that adhered to the client’s precise spatial and technical specifications. The new transformer assembly was equipped with a Tec Systems T154 temperature controller, known for its advanced thermal management capabilities, which provided accurate temperature monitoring and control. Additionally, we incorporated the ADIT AD-12A0 relay, featuring ZORC technology for superior neutral earthing and surge protection. This combination of modern components not only ensured compatibility with the existing setup but also provided significant enhancements in diagnostic and protective functions.
Impact:
The new transformer assembly markedly improved the system’s reliability and operational efficiency. The advanced temperature control mechanisms and enhanced protection features led to a reduction in maintenance interventions and mitigated the risk of system failures. As a result, the client experienced a more stable and reliable power supply, lower maintenance costs, and extended operational longevity of the transformer, ensuring continuous and efficient power distribution.
Retrofitting Variable Speed Drives (VSDs) with External Cooling in Existing Panels
Challenge:
The control panel responsible for managing four 350kW motors was not equipped with Variable Speed Drives (VSDs), resulting in high energy consumption and operational inefficiencies. Space constraints within the control panel prevented the installation of conventional VSDs, exacerbating the challenge. The lack of VSDs meant that the motors operated at fixed speeds, leading to inefficient energy use and higher operational costs.
Solution:
We tackled this challenge by modifying the control panel door to accommodate panel-mounted VSDs while maintaining the panel’s existing footprint. To manage the heat generated by the VSDs, which amounted to 6,674 watts, we collaborated with a specialist cooling OEM to design a bespoke cooling system. This system featured custom ducting solutions to ensure optimal heat dissipation and prevent overheating of the VSDs. The innovative cooling design maintained safe operating temperatures and improved overall system efficiency.
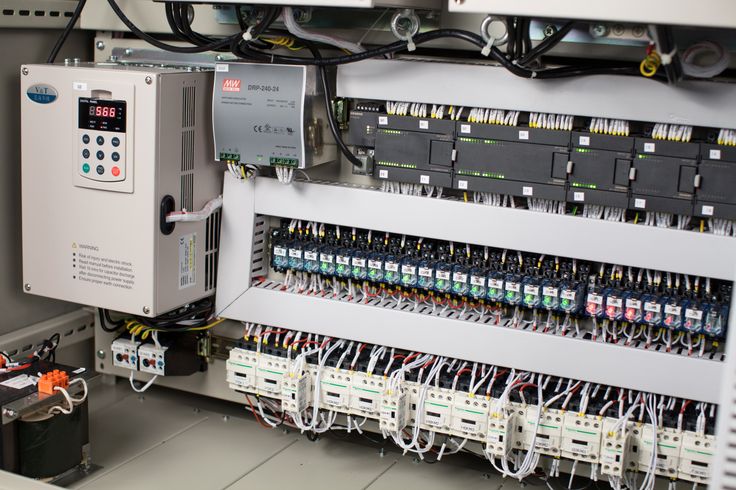
Impact:
The retrofit not only enhanced the energy efficiency of the motor control system but also improved the operational reliability of the VSDs. The effective cooling system prevented overheating, thereby extending the lifespan of the VSDs and associated components. This solution resulted in substantial energy savings, improved system efficiency, and reduced maintenance downtime, ultimately leading to more reliable and cost-effective operations.
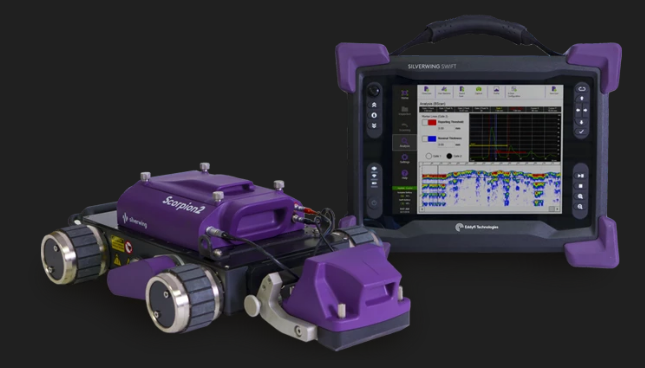
Robotic Corrosion Detection in Carbon-In-Leach Tanks
Challenge:
Traditional methods for detecting corrosion in carbon-in-leach tanks were labour-intensive and prone to missing hidden damage. Visual inspections required scaffolding, which was costly and time-consuming, while manual ultrasonic testing (UT) gauges provided incomplete data, leading to inaccurate Risk-Based Inspection (RBI) calculations. The challenge was to find a more efficient and accurate method for corrosion detection that could provide comprehensive and reliable data.
Solution:
We introduced a robotic ultrasonic inspection crawler designed to address these limitations. The crawler could detect corrosion in materials with thicknesses ranging from 4.7 to 100 mm, providing a detailed assessment of the tanks’ condition. Equipped with a long umbilical cable, the crawler offered enhanced manoeuvrability, allowing it to access hard-to-reach areas without the need for scaffolding. The robotic system provided high-resolution data on corrosion rates and locations, which improved the accuracy of RBI calculations and enabled more effective maintenance planning.
Impact:
The implementation of the robotic inspection crawler significantly reduced the time and costs associated with corrosion inspections. The enhanced data accuracy facilitated better planning of maintenance activities, reducing unplanned downtime and improving the overall operational efficiency of the tanks. The solution also improved safety by eliminating the need for scaffolding and manual inspections in hazardous environments, resulting in a more efficient and safer inspection process.
Pump Station Control Panel with Variable Speed Drives and PLC Integration
Challenge:
The existing control panel for managing a water supply network over 100km was corroded and outdated, resulting in inefficiencies and unreliability. The panel’s lack of modern control capabilities hindered the system’s performance and required replacement to improve energy efficiency and operational reliability.
Solution:
We collaborated with a specialist to design and implement a new control panel that featured five Danfoss 30kW VSDs for optimal control of the Flygt pumps feeding the water supply network. The new panel was equipped with advanced PLC components, allowing for remote monitoring and control of the water supply system. Additional features included bypass contactors and level control relays to ensure smooth and reliable operation. The transition to a soft starter configuration further optimized energy consumption and reduced operational stress on the pumps.
Impact:
The new control panel significantly improved the energy efficiency and reliability of the pump station. The advanced control capabilities allowed for better management of the water supply network, reducing wear and tear on the pumps and extending their operational life. The upgrade resulted in lower operational costs, improved control over water distribution, and enhanced overall system performance, leading to more effective and efficient water management.
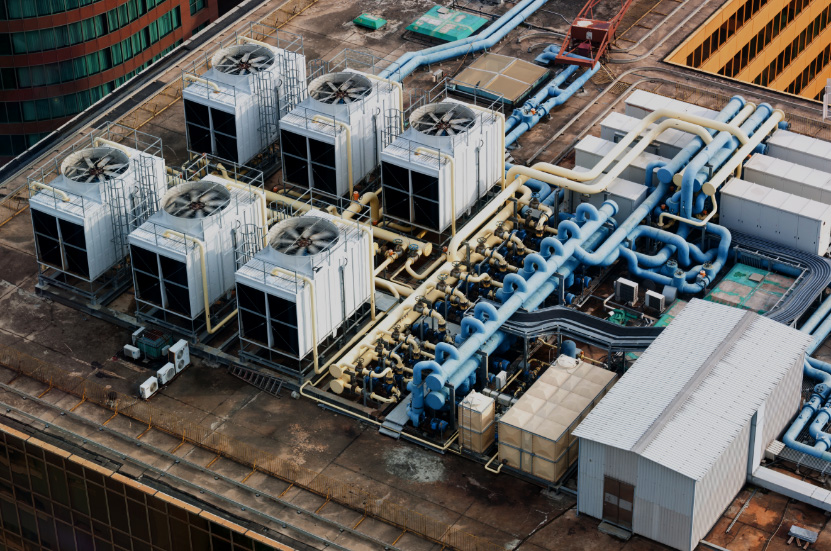
Cooling Optimisation for 1000kW Generators
Challenge:
The cooling fans on a fleet of 20 x 1000kW generators were inadequate, leading to frequent overheating issues and increased maintenance needs. The underperformance of the cooling system affected generator efficiency and reliability, resulting in operational disruptions and higher costs.
Solution:
We partnered with a UK-based fan manufacturer to design and install new, high-efficiency cooling fans with optimized pitch angles to improve airflow and pressure. The new fans were specifically engineered to meet the operational requirements of the generators, providing a customized solution to address the cooling deficiencies. The upgrade involved replacing the existing fans with more efficient models that enhanced cooling performance and reliability.
Impact:
The upgraded cooling system resulted in improved generator performance by effectively preventing overheating and reducing maintenance requirements. Enhanced cooling efficiency contributed to better fuel consumption and lower operational costs. The solution also reduced the frequency of repairs and downtime, leading to increased operational stability and cost savings for the client.
Bespoke Cleaning Solution for Heat Exchanger Tubes
Challenge:
Heat exchanger tubes, measuring 10mm in diameter and 4.5m long, frequently experienced blockages due to scale build-up from caustic soda and calcium deposits. Traditional cleaning methods, such as pressure washing, were ineffective and posed risks of damaging the tubes.
Solution:
We collaborated with an OEM to develop custom stainless-steel cleaning brushes designed specifically for the dimensions and material of the heat exchanger tubes. These brushes provided a thorough cleaning solution while ensuring the integrity of the tubes was preserved. The bespoke design addressed the specific cleaning challenges associated with scale build-up and extended the operational life of the heat exchangers.
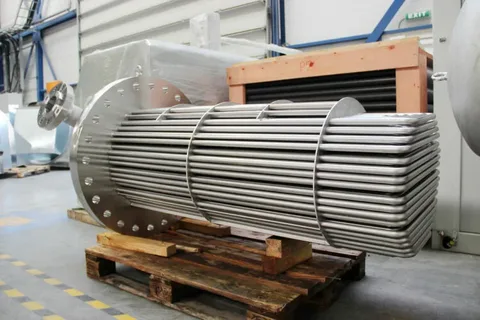
Impact:
The custom cleaning solution significantly improved the effectiveness of routine maintenance and reduced the frequency of blockages. By preventing damage to the tubes and extending their service life, the solution contributed to lower maintenance costs and improved system performance. The client benefited from fewer outages and a more efficient heat exchange process, resulting in enhanced operational reliability.
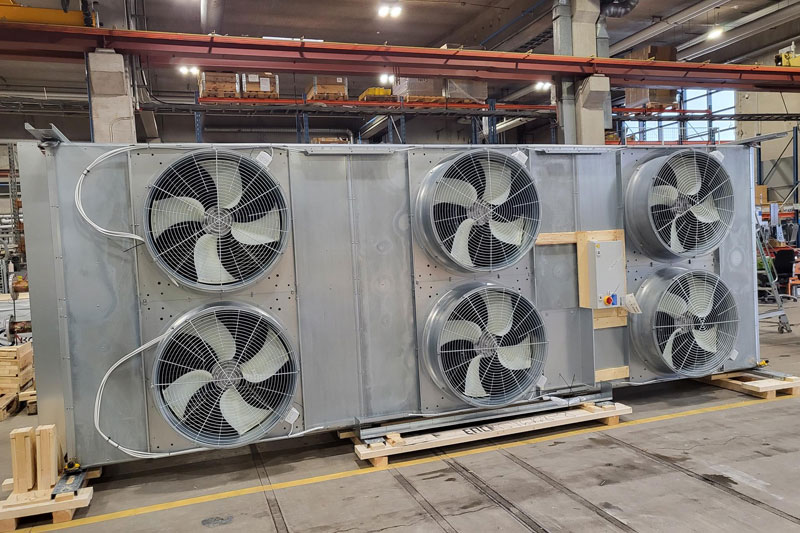
Integration of Variable Speed Drives into Cooling Radiators
Challenge:
The cooling radiators in a client’s plant were manually operated, leading to inefficient power consumption and suboptimal cooling performance. The manual operation resulted in higher energy costs and less effective cooling, impacting overall plant efficiency.
Solution:
We collaborated with an OEM to retrofit the cooling radiators with Variable Speed Drives (VSDs). The VSDs enabled automatic adjustment of fan speeds based on real-time cooling demands, optimizing power usage and enhancing cooling efficiency. The integration provided a more responsive and energy-efficient cooling system, addressing the inefficiencies of manual operation.
Impact:
The automated cooling system achieved substantial energy savings by reducing power consumption and improving overall efficiency. The reduction in operational costs and carbon footprint contributed to a more sustainable and cost-effective plant operation. The client experienced enhanced cooling performance, lower energy expenses, and a more efficient system overall.